Choosing the right anti-corrosion protection is crucial for a successful outcome
A cable support installation is considered to be a long-lasting solution and the life expectancy is dependent on the environment in which it is placed. A thorough investigation of the setting in terms of corrosion, pollution, humidity, salt, sanitary regulations etc will help you make the best choice. Our range of cable ladders and accessories covers all types of surface treatments, enabling a reliable, cost-efficient and long-lasting cable support solution.
C1 Very low
Indoor environments: Schools, shops, hotels, offices, sports halls etc.
- Very low environmental corrosion.
- Heated areas.
- Arid atmosphere.
- Insignificant quantities of pollutant.
- ISO 2081.
Recommended materials:
Electro-galvanized (EG) or Pre-galvanized steel (PG)
C2 Low
Partly outdoor environments: Industries, sports halls, warehouses, shops, rural outdoor areas etc.
- Low environmental corrosion.
- Non-heated areas with fluctuating levels of temperature and humidity.
- Few instances of condensation and low levels of airborn pollution.
- SS-EN 10346
Recommended materials:
Pre-galvanized steel (PG)
C3 Average
Indoor- and outdoor environments: Urban and light industrial areas, breweries, dairies, laundries etc.
- Average environmental corrosion.
- Areas with average levels of humidity and some airborn pollution caused by production processes.
- Atmospheres containing some salt or average levels of airborne pollution.
- EN-ISO1461/EN 10346 (Z+)
Recommended materials:
Hot dip galvanized steel (HDG) or Zinc+ (Z+)
C4 High
Indoor- and outdoor environments: Chemical plants, industrial and coastal areas, swimming pools, farms, dockyards etc.
- High environmental corrosion.
- Areas with high levels of humidity and considerable airborn pollution.
- Atmospheres with average salt content or discernible levels of airborne pollution.
- EN-ISO1461
Recommended materials:
Hot dip galvanized steel (HDG) or Zinc+ (Z+)
C5 Very high
Indoor- and outdoor environments: Chemical and heavy industries, tunnels, swimming pools, dockyards etc.
- Very high (industrial) environmental corrosion.
- Areas with almost permanent condensation, large quantities of airborn pollution, high levels of humidity and aggressive atmospheres
- EN 1.4301 acc. to EN 10088/AISI 304
Recommended materials:
Zinkpox (ZP) or Stainless steel AISI304L
CX Extreme
Indoor- and outdoor environments: Heavy industries, coastal and offshore areas, purifying plants etc.
- Very high (marine) environmental corrosion.
- Areas with almost permanent condensation and large quantities of airborn pollution. Atmospheres with high salt content.
- EN 1.4404 acc. to EN 10088/AISI 316L
Recommended materials:
Stainless steel AISI316L or FRP/GRP
The life expectancy of a cable support system is dependent on the environment in which it is placed. Therefore, it is important to establish the corrosive properties of an environment to ensure that the right treatment and the right material are chosen. Do not use components finish above of the corrosion class targeted. The table below shows various corrosion classes. As a guide, we have included the surface treatment recommended by Wibe Group for the different classes.
We briefly outline the various surface treatments and materials. As regards environmental corrosion, a steel design component can usually be assigned to one of the corrosion classes (C1 to CX) as shown in table A. Reference values for the average level of corrosion in steel and zinc are given in table B. The corrosion classes comply with those stipulated in SS-EN ISO 12944-2.
Table A
Corrosion classes as stipulated by SS-EN ISO 12944-2 with atmospheric corrosion levels and examples of the environment in which they are most suitable for use.
Corrosion class | Environmental corrosion | Examples of typical environments in temperate climates (informative) | Wibe Group designation | ||
Outdoors | Indoors | ||||
C1 | Very low | Heated areas with arid atmosphere and insignificant quantities of pollutant, e.g. offices, shops, schools and hotels. | Electro-galvanized DIN 50961/ISO 2081 |
||
C2 | Low | Atmospheres with low levels of airborne pollution. Rural areas. | Non-heated areas with fluctuating levels of temperature and humidity. Few instances of condensation and low levels of airborne pollution, e.g. sports halls and warehouses. | Pre-galvanized Z 275 in accordance with EN 10346 |
|
C3 | Average | Atmospheres containing some salt or average levels of air-borne pollution. Urban and light industrial areas. Areas affected by coastal conditions. | Areas with average levels of humidity and some airborne pollution resulting from production processes, e.g. breweries, dairies, laundries. | Hot-dip galvanized after manufacture in accordance with EN-ISO 1461 | Zinc+ coating |
C4 | High | Atmospheres with average salt content or discernible levels of airborne pollution. Industrial and coastal areas. | Areas of high humidity and considerable airborne pollution as the result of production processes, e.g. chemical plants, swimming pools and dockyards. | ||
C5 | Very high | Industrial areas with high humidity and aggressive atmosphere, and coastal areas with high salinity | Buildings with almost permanent condensation and with high pollution | Zinkpox® HDG+powder coating |
|
Stainless steel EN 1.4301/AISI 304 |
|||||
CX | Extreme | Offshore areas with high salinity, industrial areas with extreme humidity, and aggressive atmospheres, sub-tropical or tropical atmospheres. | Industrial buildings with extreme humidity and aggressive atmosphere. | Stainless steel EN 1.4404/AISI 316L GRP* |
*see catalogue Mita Flex for GRP offer
Table B
Mass losses for zinc in various corrosion classes
Corrosion class | Mass loss per surface unit and thickness reduction (1 year of exposure)1 | |
Zinc | ||
Mass loss (g/m2) | Thickness reduction (μm) | |
C1 | < 0.7 | < 0.1 |
C2 | > 0.7 to 5 | > 0.1 to 0.7 |
C3 | > 5 to 15 | > 0.7 to 2.1 |
C4 | > 15 to 30 | > 2.1 to 4.2 |
C5 | > 30 to 60 | > 4.2 to 8.4 |
CX | > 60 to 180 | > 8.4 to 25 |
*Corrosion speed is generally higher when the material is first exposed
Surface treatments
Wibe Cable Ladders - Technical and material data
Specification
Cold formed steel: DX5xD acc. to EN 10346, DC0x acc. to EN 10130, DD1x acc. to EN 10111 Structural steels: S235 and S355 acc. to EN 10025-2 AISI 316L acc. to EN ISO10088-2
Density:
7.7-7.85 kg/m3
Surface treatment:
• Pre galvanized (>20 μm): EN 10346
• Hot-dip galvanized (55-70 μm): EN ISO 1461
• Zinc+ (>25 μm): EN 10346 • Zinkpox, hot-dip galvanized (55-70 μm) + polyester coating, white RAL9010
• Pickled (Stainless steel), except KHZSP ladder range
Resistance to impact:
20 J (IEC 61537)
Temperature range:
From –40°C to +120°C.
Electro-galvanized
Products are manufactured in accordance with ISO 2081. Such products are intended for use only in warm, dry areas with negligible pollutant levels.
Pre-galvanized
Products are manufactured from Z 275 pre-galvanized sheet steel in accordance with SS-EN 10346. Under normal conditions, surface sections created during cutting and drilling will repair themselves, providing superb anti-corrosion protection.
Hot-dip galvanized
Wibe Group has one of the most modern hot-dip galvanization plants in the Nordic countries. The hot-dip process is continuous, guaranteeing a high and even quality. The manufactured products are hot-dip galvanized in accordance with EN-ISO 1461:2009 whilst nuts and bolts are hot-dip galvanized in accordance with SS-EN ISO 10684. This form of galvanization affords very good value-for-money anticorrosion protection in atmospheres with a pH value of between 6 and 13. However, in acidic environments where pH levels fall below 6 and in alkaline environments where the pH value exceeds 13, the protective zinc layer breaks down relatively quickly. When cuts/perforations or other kind of operation that damage or remove coating in HDG items suitable to be installed in aggressive corrosion class, must be repaired with a zinc rich paint.
Zinc+
Zinc+ surface treatment for some accessories (EN 10346) with a metallic Zinc-based coating containing aluminium and magnesium that offers ultimate corrosion resistance in aggressive environments (e.g. chloride & highly alkaline). In many cases a good alternative to hot-dip galvanization. Excellent surface finish with self-repairing protection of cut edges (galvanic protection).
Zinkpox®
The Zinkpox® method involves applying a homogenous polyester coating to the zinc layer. Besides resisting light-initiated degeneration and weathering, this powder coating has excellent mechanical properties as regards impact resistance and adhesion. It is also resistant to most chemicals. Compared to hot-dip galvanizing, applying a polyester coating to the zinc layer more than doubles the service life of treated components. The zinc layer prevents the development of filiform corrosion. This might otherwise degrade the coating. Consequently, the polyester coating is subject only to atmospheric attack and thus protects the zinc layer. The certified coating plant that treats our components uses a modern and environment-friendly process. Before powder coating, the galvanized components undergo meticulous pre-treatment. This ensures superb adhesion. In addition to extremely good corrosion protection, the Zinkpox® method also offers a choice of colours. Powder coating is a very environment-friendly way of achieving a coloured surface. Because the coating contains no solvents, it has largely replaced solventbased liquid coatings. Where installations are visible, cable ladders and fittings can be finished in a coating that matches the surrounding décor.
Stainless steel
Products manufactured in accordance with AISI 304 acc. to ASTM / 1.4301 acc.to EN 10088-3 or /AISI 316L acc. to ASTM / 1.4404 acc. to EN 10088-3 are designed for use in highly aggressive environments, either indoors or outdoors, on industrial sites where there are high levels of potent airborne pollution such as in certain chemical industries, cellulose-related industries, refineries or artificial fertilizer factories, high humidity tunnels, etc. Stainless steel products are also ideal for use in environments where special hygiene requirements are in force, such as dairies, abattoirs, other food industries and pharmaceutical factories.
Stainless steel AISI 304 or AISI 316L
The deciding factor in choosing between stainless steel AISI 304 or AISI 316L is the aggressiveness of the environment in which it is to be used, and for this atmospheric chlorine content plays a significant role. Environments with a high chlorine content, coastal areas being a prime example, are aggressive and usually require the use of AISI 316L materials. When assessing the needs of factories, consideration should be given to the materials previously used to suspend equipment such as pipe tubing, and from this determine whether stainless steel AISI 304 or AISI 316L material is required.
To consider when installing Stainless Steel Cable Laddes
1. Transport/handling: Make sure that no iron objects come into contact with the stainless steel products.
2. Storing: Never store stainless steel products close to where iron products are machined, for example close to cutting and grinding operations
3. Welding: Welding during installation should be avoided where possible. If welding must be performed, make sure that only methods suitable for stainless steel are used.
4. Tools: When cutting or grinding, always use cutting wheels and grinding tools which are free from iron. Do not use tools that have been previously used for cutting or grinding products containing iron. When drilling, use an HSS-drill. To maximize the useful life of the drill, employ a cooling fluid during drilling. When installing, conventional assembly tools can be used. However, when using a nut tightener, ensure that the thread is first lubricated to prevent jamming.
Never mix untreated or galvanized products with stainless steel.
5. Measures: If a blue annealing appears when cutting, grinding or drilling, re-move it with pickling paste, making sure that the paste is then carefully washed away with water. If selective corrosion appears it can be removed by:
a) Washing away with water (high-pressure if possible).
b) Polishing with a cleaning cloth or a fine emery paper (wet or dry) and washing with water.
c) Grinding with a fine-grained wheel and washing with water.
d) Pickling with pickling paste, making sure that the pickling paste is then carefully washed away with water.
6. When using pickling paste or similar products, always study the safety code for the product prior to use.
Download the information
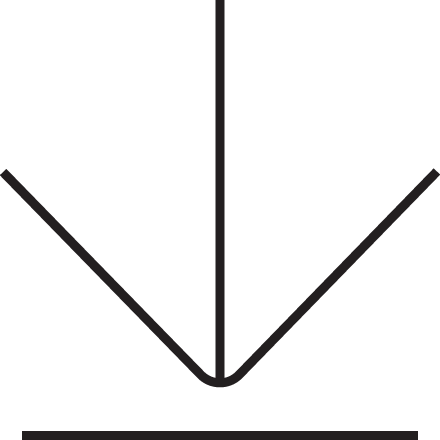